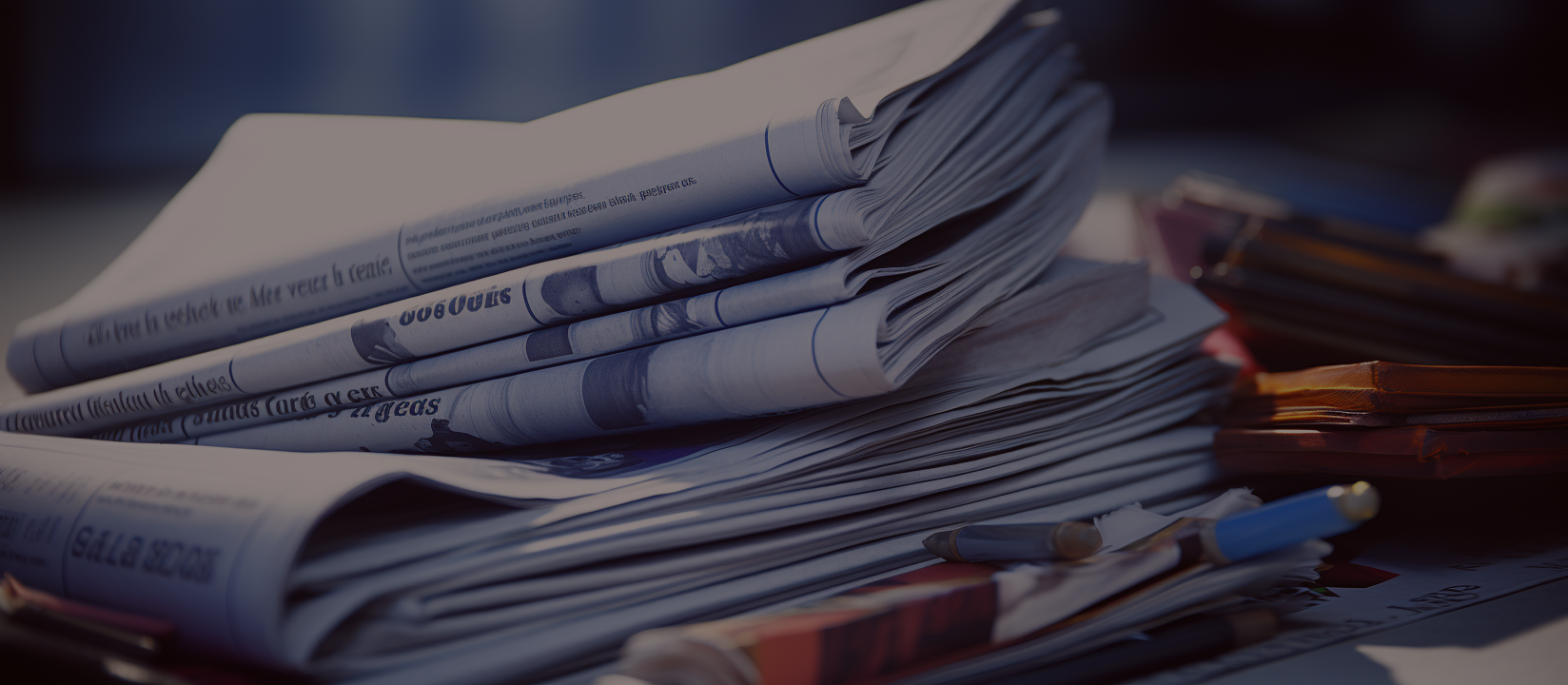
¿Cómo hacer coincidir el brazo del robot con la máquina de moldeo por inyección?
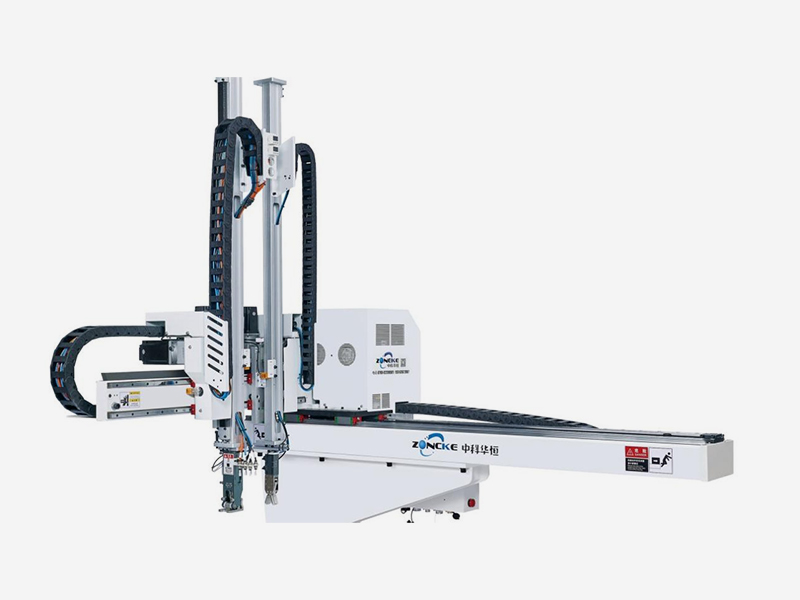
Hacer coincidir un brazo de robot con una máquina de moldeo por inyección implica varios pasos clave para garantizar la compatibilidad, la eficiencia y la seguridad. Aquí hay una guía del proceso:
1. Determinar la aplicación y la funcionalidad
Pick-and-Place: si el brazo del robot se usa para manejar piezas (insertar o eliminar), evalúe el alcance del robot, la capacidad de carga útil y la velocidad.
Ciclo de moldeo: considere el tiempo de ciclo de la máquina de moldeo y cómo se integrará el brazo del robot con él para evitar demoras.
Complejidad por parte: si las piezas tienen forma compleja, el brazo del robot debe tener un alto grado de libertad o herramientas especializadas (como las puntas o las tazas de succión).
2. Capacidad de carga útil y alcance
Capacidad de carga útil: asegúrese de que el brazo del robot pueda manejar el peso de las piezas que se recogen o colocan. Esto depende del tamaño y el material de la parte moldeada.
Alcance: el robot debe tener un alcance suficiente para acceder al área de molde de la máquina de moldeo por inyección y descargar piezas de manera eficiente sin obstrucción.
3. Coordinar la integración del sistema
Coordinación de la máquina: el sistema de coordenadas del brazo del robot debe alinearse con la máquina de moldeo por inyección (IMM). Esto incluye configurar el robot para elegir piezas de ubicaciones específicas (por ejemplo, la cavidad del moho o el área de enfriamiento).
Sincronización: el robot debe sincronizarse con el ciclo de IMM. Por lo general, se envía una señal cuando se abre el molde, y el brazo del robot debe actuar rápidamente para eliminar la pieza. Esto podría involucrar a los PLC (controladores lógicos programables) para sincronizar los ciclos.
4. Interfaz y comunicación
Compatibilidad del controlador: el controlador del robot debe poder comunicarse con el sistema de control de la IMM. Esto puede requerir integración a través de protocolos comunes como Modbus, Ethernet/IP o Profinet.
Coordinación del tiempo del ciclo: asegúrese de que el robot esté programado para comenzar su funcionamiento una vez que se complete el ciclo de moldeo por inyección, asegurando la eliminación de piezas suaves y el tiempo de inactividad mínimo.
5. Consideraciones de seguridad
Recintos de seguridad: dependiendo de la velocidad y el movimiento del robot, se deben instalar barreras de seguridad o cortinas de luz para proteger a los operadores de piezas móviles.
Paradas de emergencia: la integración de las funciones de parada de emergencia entre el IMM y el brazo del robot es crucial para la seguridad general.
6. Efectores finales
PRISIONES O CUPAS DE SUCCIÓN: Elija el efector final correcto en función de la geometría de la pieza. Para piezas pequeñas o delicadas, las pinzas a base de vacío pueden ser más adecuadas, mientras que las piezas más grandes y resistentes pueden necesitar pinzas mecánicas.
Personalización: si las piezas tienen una forma irregular, se pueden requerir herramientas personalizadas para garantizar un manejo seguro y eficiente.
7. Integración de software
Programación del robot: configure la programación de robot para que coincida con el ciclo del Imm. Esto incluye ajustar los movimientos para precisión, velocidad y evitar colisiones.
Monitoreo y ajuste: algunos sistemas permiten el monitoreo remoto de la IMM y el robot, por lo que se pueden hacer ajustes en tiempo real si es necesario.
8. Instalación física
Montaje del robot: instale el robot en una plataforma de montaje adecuada cerca del inm. Un método común es montar el robot en el IMM en sí o en un pedestal separado.
Gestión de cables: enruta correctamente los cables y las mangueras (si las hay) para que el brazo del robot se asegure de que no interfieran con los movimientos de la IMM y permanecen protegidos contra daños potenciales.
9. Prueba de ciclo
Carreras en seco: realice corridas secas para verificar la interacción del robot con el Imm. Pruebe los movimientos, la velocidad y la eficiencia del robot de manera controlada antes de comenzar la producción completa.
Ajustes: realice los ajustes necesarios a la velocidad, los tiempos del ciclo o las herramientas según los resultados de la ejecución seca.
10. Optimización y mantenimiento
Optimización: después de la instalación y las pruebas iniciales, controle continuamente el sistema para asegurarse de que los tiempos de ciclo estén optimizados y se minimice el tiempo de inactividad.
Mantenimiento: el mantenimiento regular y la calibración del brazo del robot y la máquina de moldeo por inyección son cruciales para la confiabilidad y el rendimiento a largo plazo.
Al igualar cuidadosamente las capacidades del Robot Arm con los requisitos de la máquina de moldeo por inyección, puede lograr una eficiencia mejorada, un tiempo de ciclo reducido y una mayor consistencia en el manejo parcial.
Blogs relacionados
- Un secador de alimentación compacta 3 en 1 y deshumidificante es una pieza especializada de equipos utilizados en industrias, como el moldeo por inyección de plástico, la extrusión o el moldeo de soplado, donde el control del contenido de humedad en las materias primas (especialmente las resinas de plástico) es crucial para garantizar la calidad del producto. Este tipo de
- El control de la temperatura del molde juega un papel fundamental en el proceso de moldeo por inyección al influir directamente en la calidad, la eficiencia y el éxito general de las piezas moldeadas. El control de temperatura del molde es esencial para lograr resultados óptimos en términos de consistencia del producto, tiempo de ciclo y energía
- Hacer coincidir un brazo de robot con una máquina de moldeo por inyección implica varios pasos clave para garantizar la compatibilidad, la eficiencia y la seguridad. Aquí hay una guía del proceso: 1. Determine la aplicación y la funcionalidad Pick-and-Place: si el brazo del robot se usa para manejar piezas (insertar o eliminar), evalúe el RO
- La implementación de un sistema de alimentación centralizado en un nuevo taller de inyección de plástico proporciona numerosas ventajas que agilizan las operaciones, mejoran la productividad y garantizan la eficiencia de rentabilidad a largo plazo. Aquí están los beneficios clave: 1. Suministro mejorado de material operacional-autor: alimentación centralizada