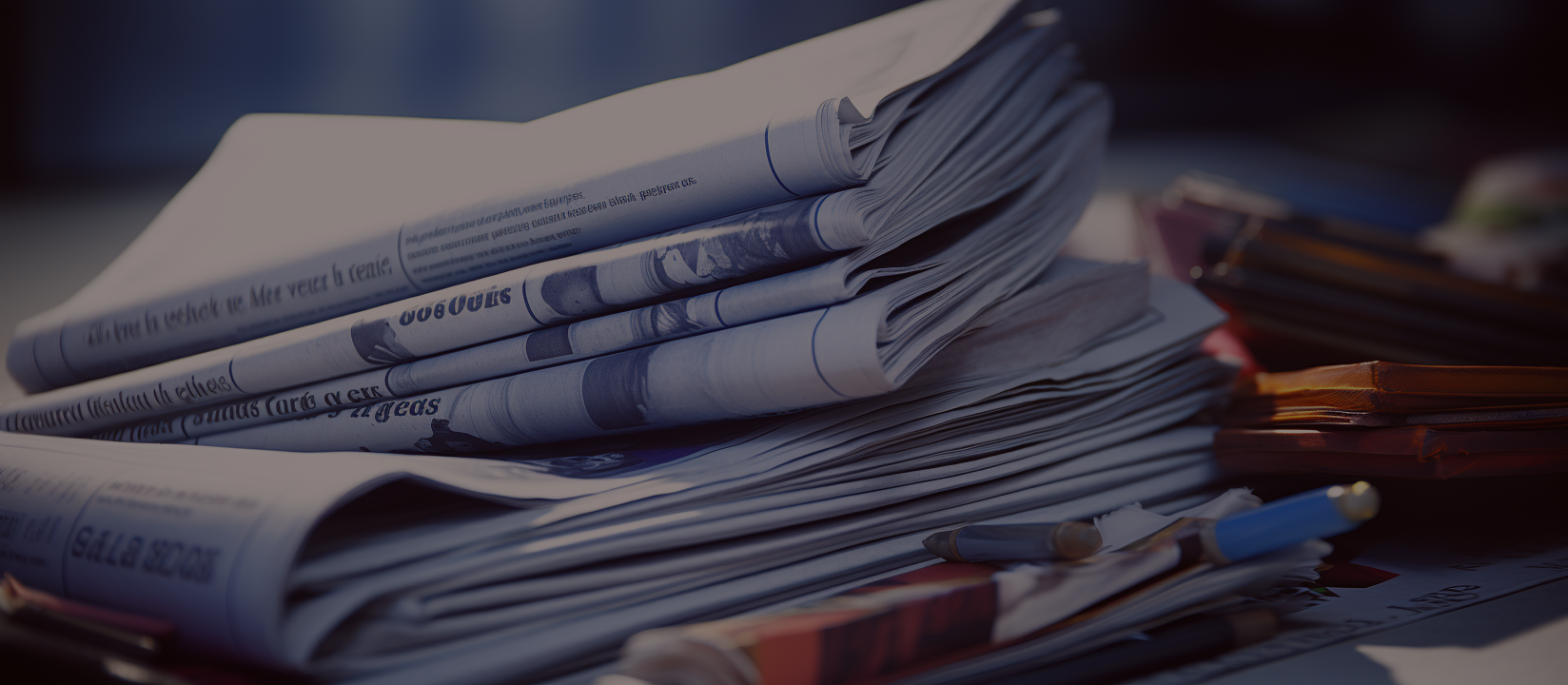
What the role of Mold Temperature Control in Injection Molding?

Mold temperature control plays a critical role in the injection molding process by directly influencing the quality, efficiency, and overall success of the molded parts. Temperature control of the mold is essential for achieving optimal results in terms of product consistency, cycle time, and energy efficiency. Here's an in-depth look at the role of mold temperature control in injection molding:
1. Enhancing Product Quality
Mold temperature directly affects the cooling and solidification of the injected plastic, which in turn influences the final product's quality. The precise control of mold temperature leads to:
Reduced Warping: When the temperature is uniform, the mold cools evenly, preventing parts from warping or distorting after being ejected.
Improved Surface Finish: A stable temperature helps achieve a smooth and consistent surface on the final product, minimizing defects like blemishes, streaks, or uneven gloss.
Fewer Surface Defects: Inconsistent cooling can lead to issues like flow marks, sink marks, or other surface defects. Mold temperature control helps minimize these problems by ensuring uniform cooling.
2. Optimizing Cycle Time
Mold temperature control is critical to improving cycle time efficiency:
Faster Cooling and Ejection: By maintaining the mold at the optimal temperature, the cooling process is accelerated, which reduces the overall cycle time. Quicker cooling means faster ejection of molded parts, resulting in higher production throughput.
Consistent Cycle Time: Consistent temperature management ensures that each injection cycle is completed with minimal variance, leading to predictable and repeatable process timings.
3. Reducing Material Stress
Plastic materials can become stressed or develop defects if cooled unevenly. Inconsistent mold temperatures can lead to:
Internal Stresses: Rapid cooling in certain areas and slower cooling in others can lead to internal stresses that result in warping, cracking, or part failure. Temperature control helps eliminate this issue by ensuring uniform temperature distribution.
Cracking or Brittleness: Parts that cool too quickly or unevenly can become brittle. Mold temperature control ensures that the plastic cools at a controlled rate, improving the durability and mechanical properties of the parts.
4. Improved Dimensional Accuracy
Mold temperature directly influences the shrinkage of the material as it cools. If the mold is not maintained at the correct temperature, it can lead to inconsistent shrinkage, which affects the dimensional accuracy of the final part. Consistent mold temperature control ensures that the part maintains its shape and tolerances, which is especially important for high-precision applications.
5. Material-Specific Temperature Optimization
Different plastic materials have different processing temperatures for optimal flow and cooling:
Thermoplastics like polypropylene (PP), polyethylene (PE), and acrylonitrile butadiene styrene (ABS) require precise mold temperatures for optimal flow and cooling.
Thermosets, which cure when heated, also require careful control over mold temperatures to ensure complete curing without defects.
Mold temperature controllers allow for precise adjustments for different materials, ensuring the mold operates at the ideal temperature for each specific polymer type. This optimizes the material properties, such as strength, flexibility, and surface finish.
6. Improved Heat Transfer Efficiency
Proper mold temperature control ensures efficient heat transfer during the molding process. Heat must be effectively removed from the mold after the molten plastic is injected to ensure the part solidifies correctly.
Efficient cooling channels (typically water or oil-based) integrated into the mold can be regulated to maintain the ideal temperature.
If the temperature is too high, the cooling rate may be insufficient, and if it is too low, the cooling may be too fast, both of which could lead to defects.
7. Reducing Energy Consumption
Modern mold temperature controllers are designed to be energy-efficient, which helps reduce the overall energy consumption of the injection molding process:
Temperature precision: Only the necessary amount of heating or cooling energy is used to maintain the desired mold temperature.
Fewer temperature fluctuations: Maintaining stable temperature conditions reduces the need for excess energy to counteract temperature swings, improving the overall energy efficiency of the molding process.
8. Minimizing Scrap and Defects
By preventing temperature-related defects, such as warping, cracking, or poor surface finishes, mold temperature control reduces scrap rates. This results in:
Less material waste: More parts meet specifications, and fewer parts are rejected due to defects, improving material efficiency.
Cost savings: With fewer rejections, both material and labor costs are reduced, enhancing profitability.
9. Consistency and Process Stability
Consistency is one of the key benefits of mold temperature control. If the mold temperature fluctuates or is inconsistent, it can cause variations in the molded parts, affecting quality. By maintaining a stable temperature, you ensure consistent mold cycles and part quality, which is critical for high-volume manufacturing.
For applications where high tolerance and consistency are required (e.g., medical devices, automotive components, electronics), mold temperature control ensures that parts are produced consistently within specifications.
10. Mold Longevity and Maintenance
Consistent temperature control also contributes to extending the lifespan of the mold:
Prevention of thermal shock: Sudden temperature changes can cause thermal stress and lead to mold damage. Proper temperature regulation minimizes this risk, preventing cracking or warping of the mold.
Reduced wear and tear: When molds are not exposed to extreme or fluctuating temperatures, the mold material experiences less wear, which helps prolong its service life and reduces maintenance costs.
Related Blogs
- Mold temperature control plays a critical role in the injection molding process by directly influencing the quality, efficiency, and overall success of the molded parts. Temperature control of the mold is essential for achieving optimal results in terms of product consistency, cycle time, and energy
- Matching a robot arm to an injection molding machine involves several key steps to ensure compatibility, efficiency, and safety. Here's a guide to the process:1. Determine the Application and FunctionalityPick-and-Place: If the robot arm is used to handle parts (inserting or removing), assess the ro