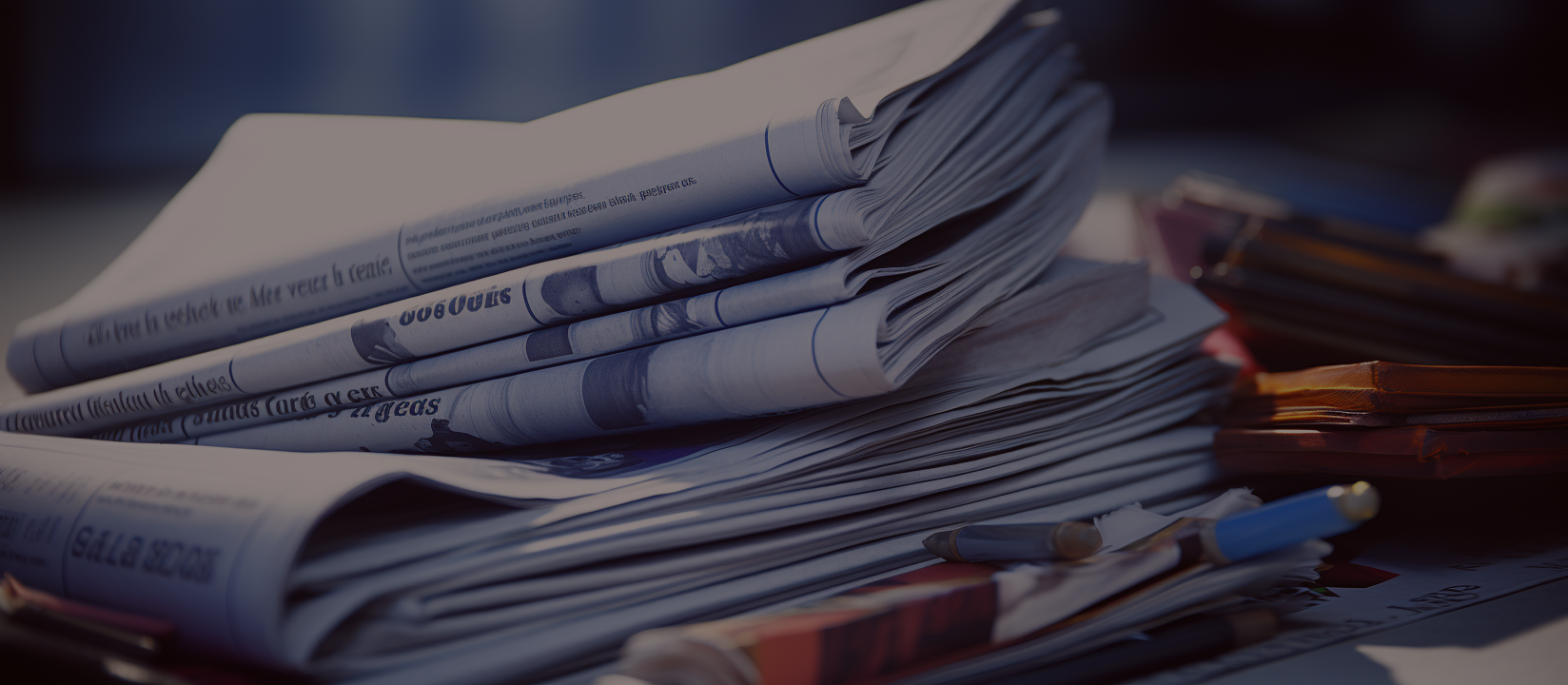
What is 3 in 1 Compact feeding and Dehumidifying Dryer?
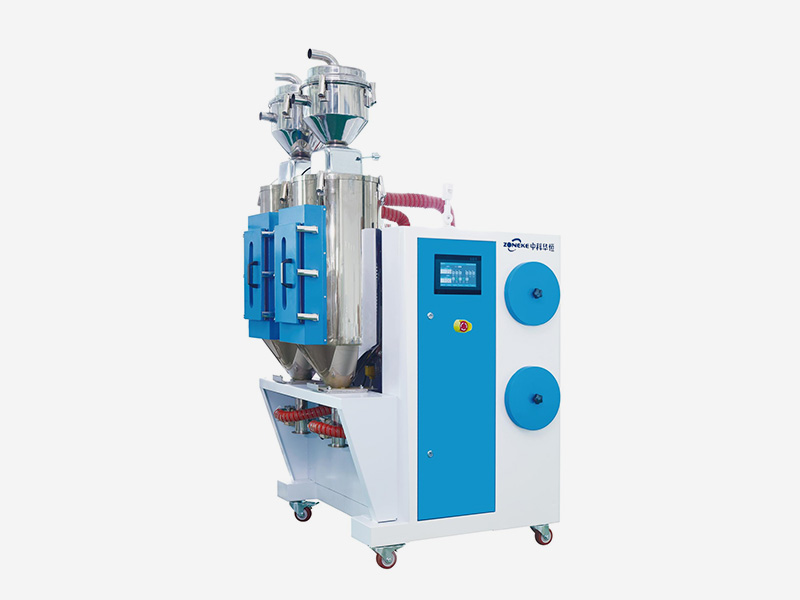
A 3-in-1 Compact Feeding and Dehumidifying Dryer is a specialized piece of equipment used in industries such as plastic injection molding, extrusion, or blow molding, where control of moisture content in raw materials (especially plastic resins) is crucial for ensuring product quality. This type of machine integrates three essential functions into a single compact unit:
1. Feeding:
The feeding function ensures a continuous supply of plastic pellets or materials into the molding or extrusion process. In many systems, a hopper loader or feed mechanism is used to move the material into the processing area.
It often includes a precision feeder that delivers an accurate amount of material, ensuring a steady and controlled flow into the injection molding or extrusion system.
Feeding is typically done by gravity or via a motorized screw, depending on the material type and processing requirements.
2. Dehumidification:
Dehumidification is an important process in drying moisture-sensitive materials. Many plastic resins (such as Nylon, PET, ABS, and PC) are hygroscopic, meaning they absorb moisture from the air. If the material is not properly dried before molding or extrusion, it can cause defects like bubbles, weak spots, or surface imperfections in the final product.
The dehumidifying part of the unit typically uses desiccant technology (a drying material like silica gel or a desiccant rotor) to remove moisture from the air. This creates a controlled environment where the plastic pellets can be dried effectively, preventing them from absorbing more moisture during the feeding process.
By dehumidifying the air around the plastic pellets, the system ensures that the materials remain at the correct moisture level, ensuring consistent performance during processing.
3. Drying:
Drying ensures that the plastic material is moisture-free before being processed. The unit heats the dehumidified air, which is then passed over the material in the drying hopper or chamber. This helps to drive out the absorbed moisture from the pellets.
The temperature is controlled to avoid overheating or damaging the plastic. This ensures the pellets are dried thoroughly and evenly, resulting in high-quality output when molded or extruded.
Key Benefits of a 3-in-1 Compact Feeding and Dehumidifying Dryer:
Space Saving: By combining feeding, dehumidifying, and drying functions into a single unit, it saves valuable space in manufacturing plants, especially in facilities with limited room or for smaller production setups.
Improved Efficiency: Integrating these functions improves efficiency by reducing the need for multiple separate machines, which streamlines workflow and minimizes setup time.
Reduced Operational Costs: A single unit performing multiple functions reduces energy consumption, maintenance needs, and capital costs compared to purchasing separate machines for each function.
Precise Control: By controlling both the feeding process and the drying environment, the machine ensures more consistent material flow and optimal moisture content, leading to better-quality molded or extruded parts.
Applications:
Injection Molding: For plastics like Nylon, ABS, and PET, the 3-in-1 dryer helps to ensure that moisture-sensitive materials are dried and fed at the correct rate, improving part quality and preventing issues like bubbles or defects.
Extrusion: In extrusion processes, materials need to be dry to ensure uniform extrusion and prevent defects like splay or weak spots. The machine provides precise feeding and drying to meet the quality requirements.
Blow Molding: Similar to injection molding, blow molding requires moisture-free materials to achieve strong, defect-free parts. The 3-in-1 dryer helps maintain consistent material properties.
How It Works:
Feeding: The raw plastic pellets are loaded into the machine and fed into the drying hopper or chamber. The feeding mechanism ensures a steady and controlled supply of material.
Dehumidification: The air around the pellets is dehumidified using desiccant or refrigeration technology to remove moisture from the air and prevent further absorption by the plastic.
Drying: The dehumidified air is then heated and circulated through the material to dry it thoroughly. The temperature is regulated to ensure optimal drying without damaging the material.
Continuous Supply: Once the material is dried, it continues to be fed into the molding or extrusion machine at the correct rate, ensuring a consistent process.
Advantages:
Compact Design: Ideal for environments where space is limited, as it consolidates three critical processes into one machine.
Consistent Material Quality: Ensures that moisture-sensitive plastics are dried to the correct level, leading to better molding or extrusion outcomes.
Cost-Effective: Reduces the need for multiple separate machines, lowering capital expenditure, operational complexity, and maintenance costs.
Related Blogs
- Mold temperature control plays a critical role in the injection molding process by directly influencing the quality, efficiency, and overall success of the molded parts. Temperature control of the mold is essential for achieving optimal results in terms of product consistency, cycle time, and energy
- Matching a robot arm to an injection molding machine involves several key steps to ensure compatibility, efficiency, and safety. Here's a guide to the process:1. Determine the Application and FunctionalityPick-and-Place: If the robot arm is used to handle parts (inserting or removing), assess the ro