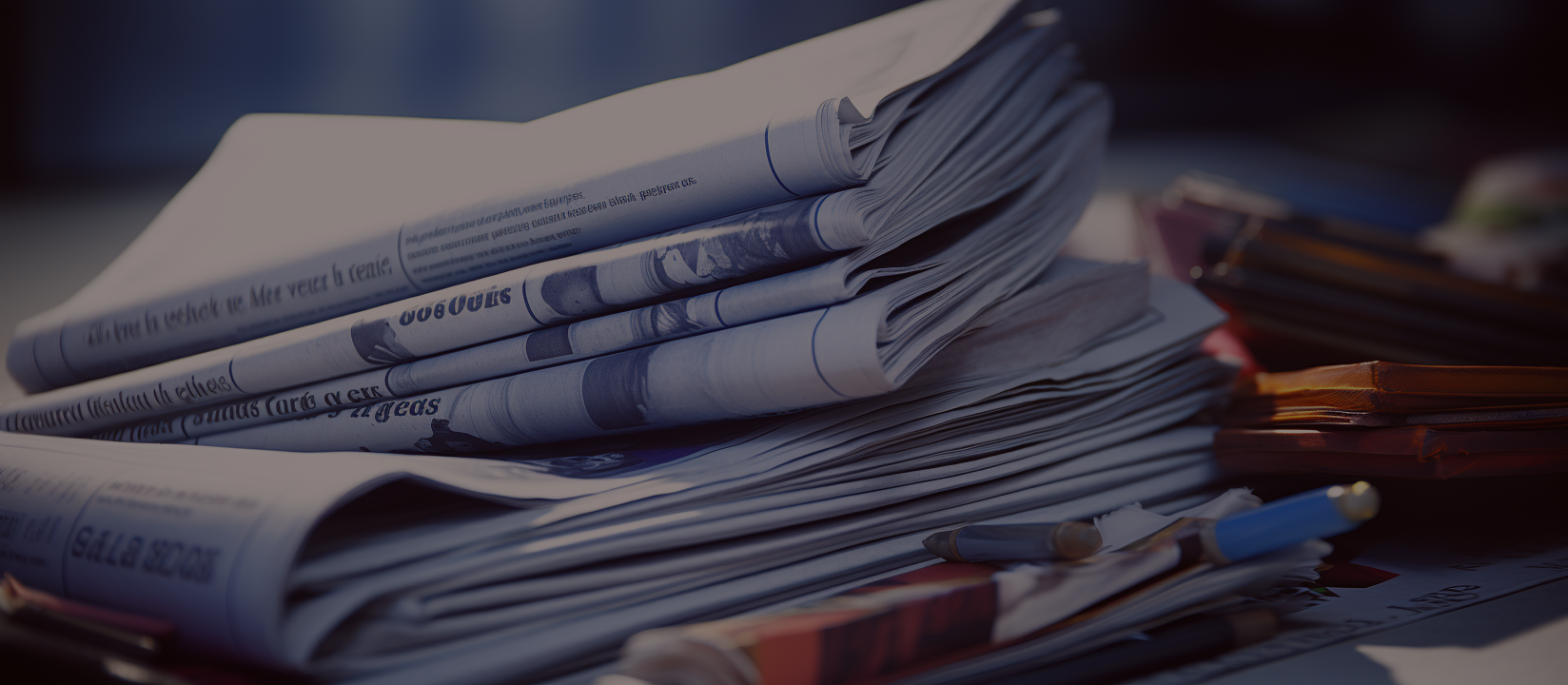
What's advantages of Centralized Feeding Systems for a new plastic injection molding workshop?
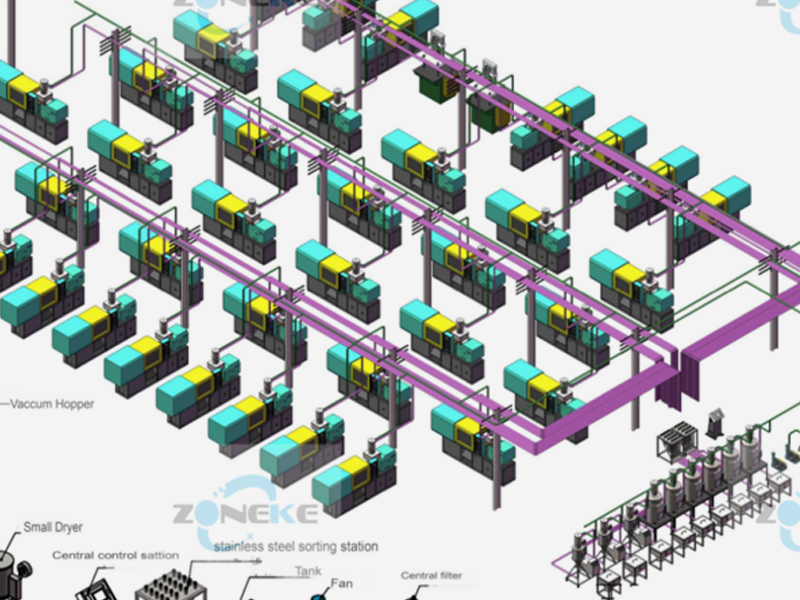
Implementing a Centralized Feeding System in a new plastic injection workshop provides numerous advantages that streamline operations, enhance productivity, and ensure long-term cost efficiency. Here are the key benefits:
1. Improved Operational Efficiency
Automated Material Supply: Centralized feeding systems continuously and automatically supply raw materials to injection machines, eliminating manual handling and ensuring uninterrupted production.
Reduced Downtime: Material handling errors, like hopper shortages or overfilling, are minimized, leading to smoother operations.
2. Enhanced Product Quality
Consistent Material Supply: Uniform feeding prevents under or over-supply issues, maintaining product consistency and quality.
Moisture Control: Integrated material drying ensures resin is at the optimal moisture level, avoiding defects like bubbles or weak points in the final product.
3. Cost Savings
Reduced Labor Costs: Automation eliminates the need for manual material transportation and loading.
Energy Efficiency: Modern systems optimize energy usage, operating only when necessary, lowering energy consumption.
Waste Reduction: Precise material handling minimizes material spillage and waste.
4. Flexibility and Scalability
Supports Multiple Machines: One system can feed multiple injection molding machines, which is ideal for workshops with varying production needs.
Future Expansion: Modular designs allow the system to expand as the workshop grows, accommodating additional machines or materials.
5. Clean and Organized Workspace
Elimination of Material Clutter: Central silos or hoppers feed directly to machines through enclosed systems, reducing storage requirements at individual machines.
Dust-Free Environment: Closed-loop conveying prevents dust or material particles from contaminating the workspace.
6. Real-Time Monitoring and Control
Centralized Management: Operators can monitor material flow, system performance, and maintenance schedules from a single interface.
Error Detection: Sensors and alarms provide immediate notifications of blockages, shortages, or system malfunctions, preventing costly downtime.
7. Compliance with Industry Standards
Improved Hygiene: Closed systems ensure raw materials are free from contamination, meeting stringent production standards.
Eco-Friendly Operations: Reduced material waste and energy-efficient components contribute to sustainable manufacturing practices.
8. Enhanced Workshop Safety
Reduced Manual Handling: Automating material movement reduces the risk of injuries related to lifting and transporting heavy loads.
Fire Prevention: Properly dried materials lower the risk of hazards associated with moisture-induced issues.
Why Centralized Feeding Systems Are Ideal for New Workshops:
Establishing a centralized system during the setup phase minimizes future disruptions and retrofitting costs.
It creates a modern, streamlined foundation for high-efficiency operations and scalability.
Related Blogs
- Mold temperature control plays a critical role in the injection molding process by directly influencing the quality, efficiency, and overall success of the molded parts. Temperature control of the mold is essential for achieving optimal results in terms of product consistency, cycle time, and energy
- Matching a robot arm to an injection molding machine involves several key steps to ensure compatibility, efficiency, and safety. Here's a guide to the process:1. Determine the Application and FunctionalityPick-and-Place: If the robot arm is used to handle parts (inserting or removing), assess the ro